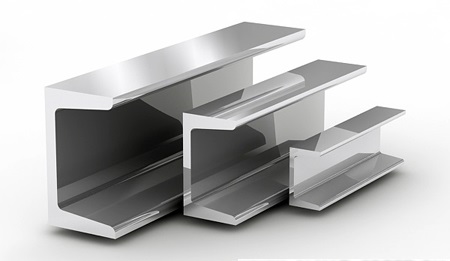
This is another type of metal rolling, the use of which allows us to solve many problems. In the general case, the aluminum channel is a pressed U-shaped profile having sharp external faces. Production is carried out from aluminum or its alloys, selected in accordance with the requirements of state standards governing the manufacture of such metal structures. The size of the shelves can be different: there are those products that have equal shelves, and those that are produced with unequal ones.

Aluminum has a lower strength than steel, however, the mass of this metal is significantly lower. Obviously, in some cases it is more advisable to use a channel, the weight of 1 meter of which is 3 times less than steel. In fact, these figures are approximate and depend on the components of aluminum and those additives that were introduced into the steel during its preparation.
Content
Applicable treatments
Today, the aluminum channel is produced in separate segments and large runs. The most popular range of lengths is from 1 to 6 m, but it is possible to produce longer ones, for example, 6.7 m. At the moment, there are several ways to classify such products, however, the most interesting is the technique, which is based on the division into types of processing:
- without heat treatment;
- annealed;
- Aged
- hardened;
- combined processing.
Below we will consider in detail the most common methods for obtaining a high-quality aluminum channel.
Heat treatment
This technology allows you to greatly modify the properties of aluminum alloy due to the fact that the change in the microstructure of the material. The main hardening in this case (without any treatment) is due to the alloying of the solid solution and the allocation of secondary phases. One of these mechanisms is dominant when preparing the raw materials from which the aluminum channel is created.
To strengthen the solid solution, the aluminum alloy is heated to the temperature at which all its components dissolve and create a homogeneous phase - aluminum, where all alloying impurities are dissolved. With increasing temperature, solubility increases, and when it decreases, it decreases. The hardening mechanism itself consists in the fact that, due to the rapid cooling of the metal, the dissolved elements remain inside the metal crystal lattice and influence it.

The distorted atomic lattice better resists plastic deformations, which means that the entire mass of the channel has a higher mechanical strength.
If hardening proceeds by isolating the secondary phases, the situation is somewhat different. Usually in this case, a certain amount of soluble chemical elements is used, for example, a combination of copper, silicon, magnesium and zinc. With a certain treatment, they combine inside the metal, forming groups of microparticles. Particles themselves are released independently even under normal conditions, but this process can be accelerated - for this, the aluminum channel is heated to 200 C.
Profile hardening
In the manufacture of aluminum products, press hardening is one of the most effective heat treatment technologies. It even surpasses hardening by separate heating. In this case, cooling is carried out to the temperature with which the profiles exit the matrix.

A prerequisite for performing such hardening is the temperature range, which must be maintained in accordance with the technology. This rule holds for both “semi-solid” and “soft” alloys. We are talking about groups 3xxx, 6xxx, 5xxx. The latter is a metal with weak doping with magnesium (less than 3%). It is allowed to process alloys 7xxx, which do not contain copper in their composition.
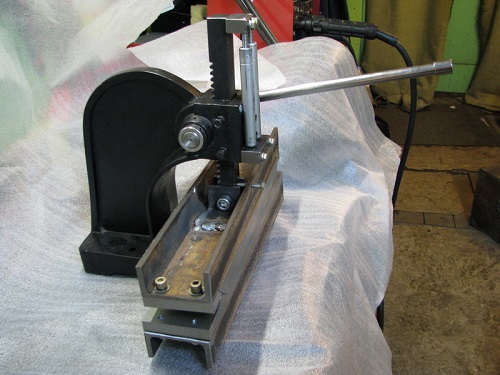
If you need an aluminum channel, you need to remember that the effect of hardening for the first two groups mentioned above is not very high. Usually this fact can be neglected and not taken into account. The final properties of the product made of 3xxx and 5xxx alloys are accepted due to the performance of the hardening, which is carried out immediately after thermal hardening.
The hardening phase for 6xxx formulations is a compound with Mg2Si. It is worth saying that all such alloys can be quenched during processing on a press. In order to fix the dissolved phrases in a solid solution, it is necessary to perform cooling at a certain speed, which is selected taking into account the characteristics of a particular alloy and should be above a certain critical point. In most cases, the aluminum channel is cooled by fans, but sometimes water or a mixture of it with air is used. The success of hardening depends on the thickness of the profile, type of alloy and chemical composition, therefore, in the case when processing of massive parts is required, the temperature difference required for hardening may not be achieved at the exit from the matrix. It is obvious that the channel, the technical conditions for which are not met, will not have the declared characteristics. To avoid such problems, the treatment is carried out in special vertical furnaces, followed by cooling in water. After hardening the aluminum profile, tensile strength is carried out by several percent in order to correct and relieve residual stresses.
The final procedure that the aluminum channel receives is aging. It can be natural or artificial. In the first case, the sample obtains the desired properties over time, which can vary over a very wide range and depends on the properties of each type of alloy. Artificial aging requires the use of special equipment - furnaces. As a rule, certain heat treatment modes are used here, which make it possible to quickly obtain a high-quality aluminum channel.
Nagartovka - cold deformation
This phenomenon occurs when performing cold deformation of the product. When plastic deformation of an aluminum alloy occurs, and its temperature is below the point at which recrystallization begins (less than 150 C), then dislocations in the metal can move and multiply. The movement and increase in the number of dislocations leads to their density increasing, and the number of bonds increasing. Each subsequent plastic deformation will require more energy, i.e. the profile becomes harder.

The channel designation includes only its dimensions, so the type of processing must be specified separately.
Note that we have described highly simplified technological processes above, however it is pointless to give them in more detail, since a professional can draw such information from a textbook or in practice. For a layman, exact numbers and the complex mechanics of chemical and physical processes are usually not of interest, the main thing is to understand how this or that aluminum channel is different.
Alas, no comments yet. Be the first!