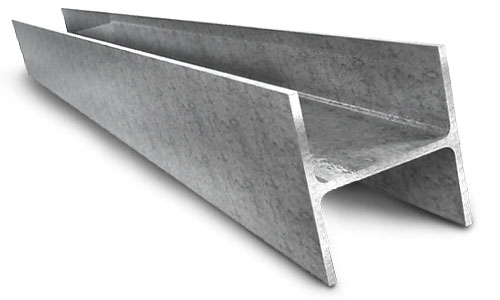
Among a huge number of the most various options of a metalwork, the I-channel is of particular interest. In fact, such a designation is not entirely correct, since the channel is the name of the U-shaped profile, but it is well-established, which means it has the right to exist. Below we will talk in detail about this type of metal, and also consider the scope of its application and variety.
What it is
An I-beam or an I-beam is one of the most common profiles. This article is about a metal beam, but you need to remember that there are wooden varieties.

Steel I-beams are made in two ways. The most common production method is hot rolled, but there is also a welded one. The welded method is used to obtain large parts or in the case when some special characteristics of the beam are required. The first production method involves the manufacture of beams that are rolled on special mills. To obtain the product, a blank is used.
In cross section, the beam is a shape close to the letter "H". The use of such structures allows you to solve several problems at once in the construction process. The first of these is that through the use of an H-shaped profile, it becomes possible to significantly reduce the mass of the structure. The second advantage is greater strength. If you compare the I-beam and the classic beam with a square profile, then the latter loses.
Where is used
Steel beams are an indispensable element of many modern structures, since in the general case when creating flat ceilings, concrete structures alone cannot provide the necessary strength and reliability. Typically, beams are used on spans of more than 7 m, but can also be used in other cases. Of course, there are concrete beams, but the latter are used in the construction of any industrial facilities. Wooden I-beams, on the contrary, are more suitable for country houses. Of course, a beam is not the only suitable option: a channel, a wooden I-beam or other products can always be used, but the ratio of strength, price and reliability for beams is the most optimal.
The main feature of the beam is that it distributes most of the tensile stresses at an angle of 45 degrees to its axis. In this case, the vertical wall acts as a zigzag grid of the farm: it distributes forces. It turns out that the reliability of the future design will be very high. On the other hand, it is possible to use other metal beams - welded.
Welded I-Beam
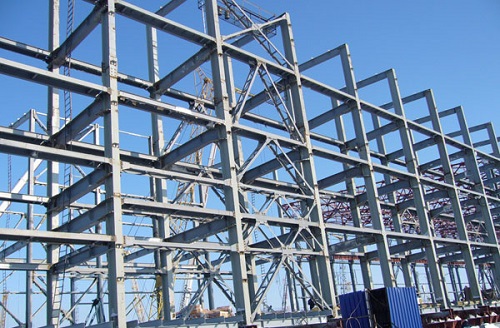
This is a kind of light metalwork having an H-shaped cross section. It is the most optimal not only in terms of reliability, but also for reasons of ease of installation. Welded structures are most widely used in the construction of civilian facilities, which require supports, bearing elements of the ceiling, etc. The use of such building materials solves one of the most difficult problems - lowering the metal consumption of the structure. I must say that the installation of a welded beam can greatly reduce the consumption of metal, because it makes it possible to choose exactly the section that is required in this case.

Channel, I-beam or welded beams are made of low alloy or carbon steel.In the first case we are talking about C255, and in the second - C345 (09G2S). The manufacture is carried out by hot or cold rolling, and the welded beam - using welded equipment, after which additional control is carried out, for example, by ultrasonic method.
The advantages of steel construction at first glance can be appreciated by any specialist, and the wide experience of their operation is the best proof of the reliability of such products:
- Weight reduction. On average, this parameter is up to 10% of the weight of all metal structures, if you replace a hot-rolled I-beam with a welded one. As mentioned above, this is due to the correct choice of the beam section.
- The ability to use different types of steels, shelves and walls. A hot-rolled product with some special characteristics will need to be ordered in advance, but with a welded one, such problems do not arise.
- It is possible to make a welded I-beam having an asymmetric section. Often, such solutions are required to simplify the design and reduce their weight.
- Welded beams can be made of any desired length, so during the construction process the costs will be minimal. Of course, there is a table of channels, beams and other metal structures, but in most cases only products with a certain length, which is the most popular in the region, are in the warehouses of suppliers.
- Welded beams increase the profitability of the project. The cost of such products is lower than that of hot-rolled products, their mass is higher, and the strength is at the required level. With the help of these metal structures it is easy to create large spans, which will lead to a decrease in the total weight of the structure, a decrease in the consumption of materials, which means it will positively affect the cost.
It should also be noted that the technology for manufacturing welded I-beams allows to obtain bimetallic beams, which belong to the special subtype and cannot be made in any other way.
What types are
The sale of channel and I-beams today is carried out by many companies, however, it must be remembered that the production of such metal structures should be carried out in accordance with GOST. So the state standard identifies several types of beams - hot-rolled and special.
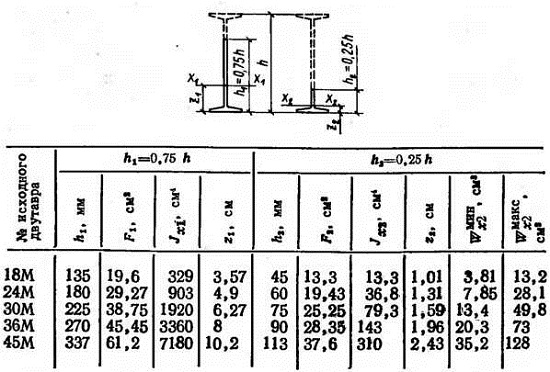
In the first case, we are talking about two types of products. One of them has sloping faces of the shelves, and the other is parallel. Beams with inclined faces are regulated by GOST 8239, which states that the angle of inclination of the faces should be in the range of 6 to 12 percent.

Unlike channels, I-beams of this type have only two classes of rolling accuracy: B - high accuracy and C - ordinary.
The deflection of the wall should not exceed 15% of its thickness, and the curvature is required less than 0.2% of the length of the product. For accuracy class “B”, the outer edges of the shelves are blunted (less than 2.2 mm), and for “C” such work is not required. Deviations by weight during production in terms of 1m3 mass should not go out of the region of minus 5%, + 3%. In some cases, the standard allows for toughening of the latter requirement, if an appropriate contract has been concluded between the manufacturer and the consumer.
I-beams with parallel sides of the shelves are made in accordance with the standard 26020. It applies to all products of this type, the height of which is within 100..1000 mm, and the shelves have a width of 55..400 mm. All such beams are divided into:
- normal
- broad-shelf;
- columned I-beams.
Standard channel, I-beam or other beams can have a length of up to 12 m, however, rolling according to GOST 26020 is made up to 24 meters.
Special beams
I-beams of this type are produced in accordance with GOST 19425. Beams for overhead tracks (M), reinforcing shaft shafts (C), and special solutions for the needs of the automotive industry belong to this category. All products are divided into two categories of accuracy - high “A” and high “B”.In this case, the slope of the inner faces is selected 12% for beams "M" and 16% for beams "C". The blunting of the outer edge of the profile is selected within 0.3 of the average thickness of the shelf.
The size or number of an I-beam indicates its relative height, expressed in centimeters. For example, I-beam No. 10 is a beam having a height of 10 cm.
Summing up, we note that above we described all types of metal I-beams used today. Our site provides fairly detailed information on other metal structures. If you require data on products such as a channel, an I-beam or a bent channel, then here you will find all the necessary information.
Alas, no comments yet. Be the first!