Today one of the most promising building materials is polycarbonate. It is not difficult to fix it to the main frame, however, even in such a situation, it is better to understand all the subtleties before installing the sheets, and not act at random.
Content
Preparatory work
When carrying out installation work, you will need to perform the following operations:
- sheet orientation
- panel cutting;
- drilling holes;
- sealing the ends of the sheets;
- point mounting of panels;
- connection of elements;
- take into account deformations due to changes in material temperature.
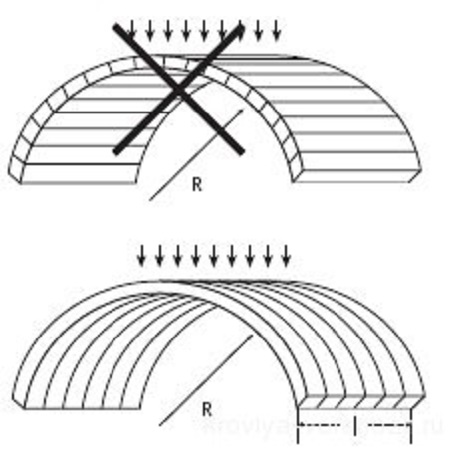
Installation of cellular polycarbonate
In cellular polycarbonate, stiffeners are located along the length of the sheet, so the panel must be positioned so that the internal channels have an exit to the outside. This is necessary to drain the condensate formed in them. When the sheets are mounted to create vertical glazing, the stiffeners must also be oriented vertically. In the manufacture of pitched structures, it will be necessary to direct the ribs along the slopes, and in the arches, the ribs are best guided along the arc.
Today, polycarbonate is made with a special protective layer that is applied to the outer surface of the sheet. On this side there is a protective film with a marking, so it is better to remove it after installing the sheet.
Cellular polycarbonate must have a strictly defined bending radius. As a rule, this parameter is specified by the manufacturer for each type of panel.
After all the necessary measurements have been completed, and the number of square meters of material recounted, you can begin to prepare the sheets.
Cutting
This operation is one of the main, since this material is supplied in the form of finished sheets, the length of which is often too long. It will be necessary to cut the panels during the construction of the greenhouse, and during the erection of the roof of the canopy or arbor.
The operation of cutting the necessary elements is very simple, since in this case there are no difficulties with polycarbonate. Here you need to use a special tool, for example, high-speed circular saws.
For cutting synthetic material, it is best to use carbide discs with small and undiluted teeth, since they will create even and accurate cut edges. The protective film must be removed last, before attaching cellular polycarbonate or after its installation, since it protects the sheets from damage during the cutting process.
During this operation, the profiles themselves must be securely fixed, since the occurrence of vibration can adversely affect the quality of the cut. After completion of work, it is better to remove chips from internal cavities. When polycarbonate is installed, they are used to drain condensate, which means that they should not create obstacles to water.
Drilling holes
To get holes, it is enough to use standard drills, however, there are a number of subtleties here. The first of them is that the holes themselves must be made between the stiffeners, and the distance from the edge of the panel to them should be more than 4 cm.
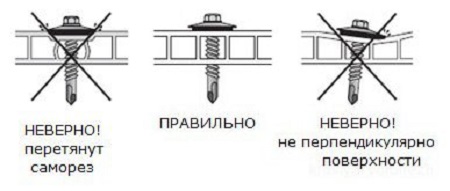
The holes in the panel must be created taking into account the fact that when the temperature of the material changes, it will deform.Typically, the installation of polycarbonate is performed with holes that are several millimeters larger than the diameter of the leg of the thermal washer. If the panel has a large length, then the holes themselves should be in the form of ellipses, the main axis of which is in the direction of the largest dimension of the sheet.
The drilling angle is allowed to be selected in the range of 90-110 degrees. Otherwise, it will not work to fix the washer horizontally and skew will occur. The mounting location itself will be unreliable, and thermal insulation in this area will deteriorate.
Sealing the ends of the panel
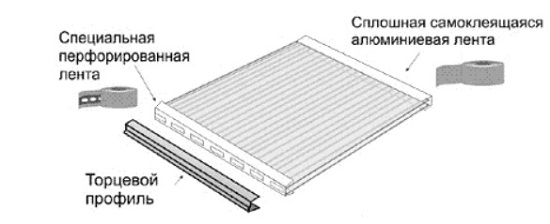
To seal the upper ends, a continuous self-adhesive tape is used. The lower ends should be pasted over with a perforated tape, which allows for the drainage of condensate.
The ends of the panels must be closed. They can not be sealed with ordinary tape, but you need to use special material. It is not recommended to seal the lower ends, since condensate is removed through them.
In order for the condensate to be removed from the structure without hindrance, you need to make several holes in the end profile. They are carried out similarly to those used for fastening the panels.
How to fasten sheets to a metal frame
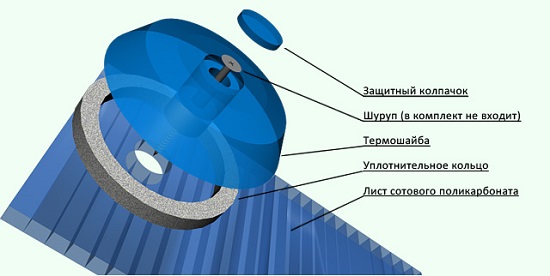
In fact, this method is suitable for any building material, only the fasteners themselves differ. Most commonly used are self-tapping screws used with special thermowells.
The thermal washer has a special leg, the length of which should correspond to the thickness of the panel. It protects the sheet from deformation, and also reduces the degree of heat loss through self-tapping screws, which are a potential "cold bridge" through polycarbonate. How to fasten panels to other materials? Yes, exactly the same: thermowells combined with self-tapping screws are a truly universal solution.
Not recommended: tighten the screws, firmly fasten the panels, and also use nails, rivets and ordinary washers. All these operations will reduce the reliability of the design.
Attachment points should be 30-40 cm apart.
Correct connection of elements

During installation, it follows that the sheets should be connected to each other using special parts - profiles. They can be one-piece and detachable.
Products of the first type are used for panels 4-6 mm, 8 mm and 10 mm, and the POLISKREP profiles belong to the second type. They can hold panels of 6-10 mm and 16 mm. Detachable profiles consist of two elements: the lower one, which plays the role of a “base,” and the upper one, a “lid” with a latch.

Connecting polycarbonate profiles allow you to create an arched or pitched structure, but they are also suitable for
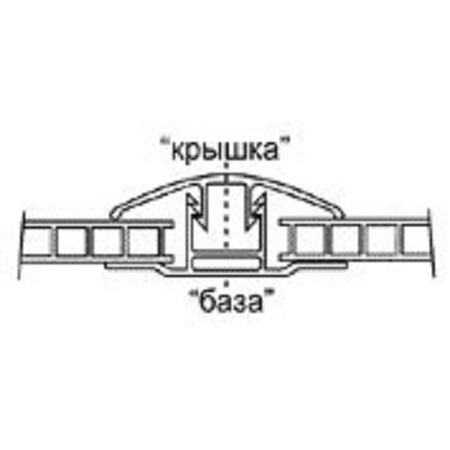
vertical sections. Each element holds two panels with a width of 50 to 105 cm, and its fastening is carried out on self-tapping screws. For joining sheets at right angles, a corner profile is suitable, and for adjoining to the wall - a special wall profile.
Mounting technology for split profile:
- In the "base" you need to drill a hole.
- Fix the “base” to the longitudinal support and lay the panels with a gap of 5 mm (necessary to compensate for thermal expansion).
- Snap on the profile cover, completing the polycarbonate installation using a wooden mallet.
Installation of monolithic polycarbonate
It can be done in two ways, however, both of them involve the use of a supporting structure that allows you to securely fix the sheet. The first method is “wet” and it is based on the use of special polymer putty. Installation of monolithic polycarbonate in this case is made with small gaps to compensate for thermal expansion. This method is great for using it together with wooden support frames.
In the case when the supporting structure is made of steel, it is necessary to use special rubber gaskets together with a sealant, which processes the clamping point from the outside and from the inside.
Dry monolithic polycarbonate installation does not require the use of any sealants and can be limited only to rubber seals. Since the system itself is not sealed, it provides for drainage that removes water.
Thermal expansion
The expansion coefficient of cellular polycarbonate is 0.065 mm per degree for each meter of the panel, so the calculation here will be quite simple. It is only necessary to estimate the maximum temperature difference during the year and multiply it by a factor. Those. when installing sheets in the middle strip (temperature range -40 .. + 50С) it should be made with a gap of 90 * 0.065 = 5.85 (mm) per meter.
If colored material is used, it must be remembered that it heats up by 10.15 ° C more, so the thermal expansion will be already 6.5 mm.
Above were considered only the main subtleties that raise questions related to the installation of cellular and monolithic polycarbonate. Of course, there is much more information in this area, but here is the necessary minimum, which will allow us to navigate this issue. Most of these tips are universal and can be used to create any structures, even if it is a roof - which will also significantly reduce the cost of installing this material.
Alas, no comments yet. Be the first!