Repairing a soft roof with roofing material is widely used for arranging and repairing the flat roof of multi-storey panel houses. Repair of a rolled roof is a roof device using the method of depositing soft bitumen-polymer compositions on a flat roof surface. Such materials are made on a fiberglass basis, impregnated with bitumen, as well as modified polymers. This type of roof is considered the third generation of soft roof development.
Roll roofing has excellent physical and mechanical properties, namely heat resistance, strength, elasticity, water resistance, increased resistance to compression, has low deformation under significant loads. Such a roof is perfectly combined with concrete and other roofing materials. Roll-up roofs have good soundproofing and sound-absorbing properties; during a shower it is practically silent.
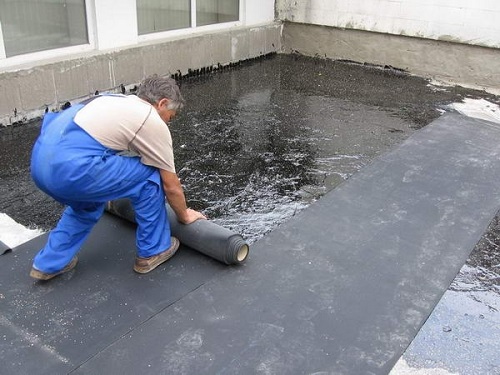
The built-up roll roof, unlike other types, is not afraid of a strong hurricane wind. An important advantage of this roll material is that it is easily transported. In industrial conditions, a bitumen or polymer-bitumen mixture is applied to the roofing material layer, and then the material is covered with a special protective layer of a special coarse grain. Often use sand, mica or slate. The bottom layer is a plastic film. The produced material can be used for deposition. The quality of the rolled roof depends on the modifiers of the bitumen mixture. Styrene-butadiene-styrene (SBS polymer) and atactic polypropylene (APP) are considered as such. These components give the material heat resistance up to +180 degrees, water resistance, fire resistance, UV resistance, flexibility.

Installation, installation and repair of a flat roll roof can be done in different seasons. Only precipitation can interfere with the performance of work. It is strongly recommended that you completely dismantle the old cover, as it may contain a certain amount of moisture, which in the future may contribute to the formation of blisters. It is because of them that puddles will form, and accordingly leaks and a reduction in the life of the roofing carpet are possible.
The correct roll roof installation technique will extend the life of up to 25 years. On the reinforced concrete surface, the rolled roof is laid by the method of melting a layer of mastic. For this, gas, propane-butane or electric burners are usually used.
If subsidence has formed on the surface, then such methods are used for leveling: if the subsidence has a recess of more than 15 mm, then after clearing the place it will be necessary to fill it with asphalt concrete, then gluing with three layers of deposited material is carried out, followed by 150 mm overlap of each layer. If the drawdown is less than 15 mm, then you do not need to peel additional layers and it will be possible to do without the use of asphalt concrete.
An air bag can also be repaired using a simpler method. It will be necessary to pierce the swollen part, release air and introduce kerosene or white spirit into the cavity. after this, the repaired area must be sealed. If the roof has small leaks at the places of installation of the drain funnel, it is necessary to replace the rigid connection between the riser and the pipe to drain the water to a movable one, and also install pipe clamps. Before applying a layer of mastic the place of sealing should be thoroughly dried and primed.
If, after a long time of operation, the roofing is free from defects and leaks, its service life can be extended. To do this, it is necessary to apply impregnation and surface protection of the material with special compounds. To impregnate the deposited roof, the composition of the mastic in percentage should be: oil bitumen - 33, solar oil - 50, white spirit - 15, sodium silicofluoride - 2.
For an additional protective layer, the composition should be as follows: petroleum bitumen - 23, solar oil - 27.5, aluminum powder - 15.5, white spirit - 25.5, asbestos - 2.5, mica - 2.5, rubber crumb - 4. Rubber crumb is introduced into the molten bitumen, slowly mixing to a homogeneous mass. Asbestos and mica, as fillers, are ground to a pulverized state, and then mixed with a bitumen-rubber binder. Into such a mass is introduced solar oil and white spirit. Later, aluminum powder is added.

The most time-consuming process in repairing a rolled roof is to remove the old cover, which often consists of 10 or more layers of roofing material. To mechanize this process, two machines are used. A multilayer carpet is cut with a rotary milling machine. The result of this machine is a seam 10 mm wide. The cover is cut into small sections of 500x500 mm. Another machine cuts these areas and removes them from the base with a knife. Waste is placed in a special container and removed from the roof. Using this equipment in one shift, you can remove about 250 mm2 of the old roof.
Large drawdowns are first leveled with asphalt, and later in two layers are sealed with roll material.
Content
Repair of a "turnkey" soft roof
Repair of a rolled roof involves:
- preparation of the roof base for subsequent installation involves cleaning from debris, dirt, water, dust removal and leveling;
- installation of a heat-insulating layer using a monolith of a plate or bulk materials;
- leveling the screed surface of the insulation;
- applying a primer layer (primer);
- the installation of a waterproofing carpet by laying the roll material and applying heated mastic;
- device of eaves overhangs, adjunctions and parapets;
- sealing roof exits under antennas, pipes, etc .;
- installation of a drainage system;
- anti-icing device for curtain rods and drains.
Most buildings with a flat roof are in need of repair. Despite the excellent physical and mechanical properties of the rolled material, in our climatic zone, over time, the soft roof becomes fragile and requires repair. Repair of the built-up roof will be required where visible cracks and defects appeared. They can be triggered by many factors. It can be wind, water, snow, air, hail, shock noise, ultraviolet, mold fungi, solutions of chemical reagents, garbage.
If through cracks are found in the upper layers of the roofing material along their width of 1 m, the roofing should be freed from crumbs or protective layer. A strip of roofing material with a width of 150-200 mm must be applied to the crack and glued on one side. Then stick the roofing in three layers so that the next one overlaps the previous one by 100-150mm. After this procedure, a protective layer is applied.
If cracks are found adjacent to the walls, it is necessary to remove or bend the protective apron and remove all layers of the deposited material, which are slightly above the crack, for convenience. Next, it is necessary to arrange an inclined transition side, to free the entire surface of the roofing carpet from crumbs or protective layer up to a width of 750 mm from the bottom of the transition side.On the protruding surface, a stub and wooden corks are arranged, to which an antiseptic wooden beam is fixed. The abutment surface below the timber must be primed and plastered with cement-sand mortar.
The bent part of the deposited carpet should be thoroughly cleaned of dust and primed. Next, hot mastic is applied to it and glued tightly to the surface. At the same time, a protective apron is nailed to a wooden beam. Using dowels, a steel strip is attached to the concrete surface, sealed with mastic, and then painted.
It is possible to determine whether repair of a built-up roof is necessary according to these signs:
- microcracks, tears, bubbles on the upper layer of the material;
- rotting and vegetation in the middle layer;
- peeling and delamination from the screed of the base of the roofing material;
- softness of gluing mastic.
Experts recommend repairing the built-up roof if there is up to 40% damage on the roof. Repair can be carried out by applying a patch or a melting seam to the defect site. Overhaul of the built-up roof is required if 60% or more of the roof is damaged.
Consequences of untimely repairs
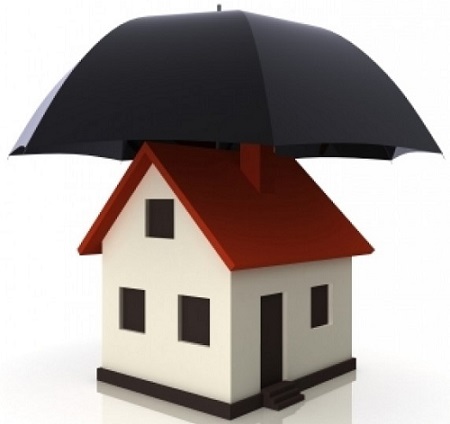
Leakage of the roof can lead to serious consequences. This can be damage to furniture, equipment, poor appearance of the building, leaking ceiling part in apartments and even before the accident of the whole building. That is why roof repairs should be of high quality, professional and timely. It includes a thorough inspection of the entire roof surface.
Roof repair with cold mastics
For such a repair, it is necessary to prepare the surface in advance: remove debris, dust, dirt and fix abutments and slopes. You will also need to make a full or partial repair of defective sections of the roof. Since this type of repair is carried out without reinforcing with fiberglass, the next step is to fill with mastic.
Repair with cold mastics with fiberglass reinforcement involves such work:
- cleaning the surface from dirt, debris, dust, correcting slopes, repairing damaged areas;
- applying the first layer of mastic;
- fiberglass reinforcement;
- applying a second layer of mastic;
- final filling with mastic;
- drawing protective aluminum paint on mastic.
Sometimes repair is used by a combined method, i.e. using cold mastics without reinforcing with special fiberglass with the deposition of a small upper layer of rolled materials. To do this, perform the same surface preparation as in previous cases. Next, the first layer of mastic is applied, reinforced with a fiberglass mesh. After that, a second layer of mastic is applied and the top layer of rolled materials is deposited.
Repair from rolled materials in one layer involves:
- surface preparation;
- priming of old coating with mastic;
- deposition of the upper layer of the roof from a soft material;
- for ventilated coatings installing flyugarok.
Types of roll roofing device and repair
- Emergency roof repair. The need for such repairs arises when detecting leaky areas or in extreme circumstances, such as extreme weather conditions or a tree falling. Often, a small part of the roof covering is replaced (5-20%).
- Roof repair. Routine maintenance of the roof is carried out regularly or if any signs of leakage or strength of individual sections are detected. This type of repair involves the replacement of 10% to 40% of the entire surface, as well as the elimination of all kinds of damage.
- Overhaul of the roof. Such repair involves a complete or partial bulkhead of the roof. Old and damaged areas are completely cut off and replaced with new ones. Overhaul involves:
- dismantling of the old coating
- dismantling of thermal insulation materials and screeds
- vapor barrier system assessment and repair
- drainage system repair
- creating a demon
- installation of thermal insulation materials
- sand-cement screed laying
- cement screed primer
- installation of roofing around funnels and aerators
- laying of the roofing in two layers at the locations of parapets and structural elements
- creation of parapets and protective aprons in places of contact (such elements are made of galvanized steel, which is coated with a polymer material).
- Roll roof device:
- installation of a storm inlet
- installation of a vapor barrier film
- installation of insulation
- installation on a heater reinforcing mesh
- laying cement screed with a thickness of 50 mm
- primer primer
- contouring primer
- surfacing with roofing material of the first layer
- adjoining with roofing material
- surfacing with roofing material of the second layer
- installation of flashlights
- mounting the clamping plate
- installation of galvanized apron
- installation of galvanized parapet.
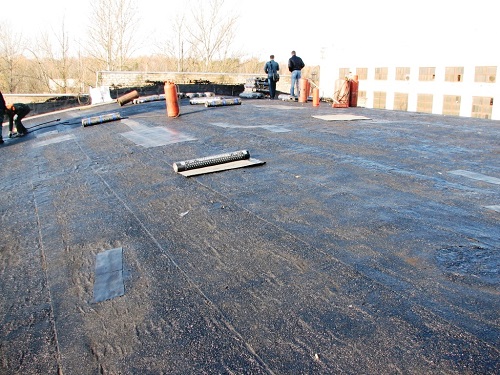
For roof insulation, bulk or plate heaters are often used. The basis of bulk insulation is expanded clay gravel. This material is used for slopes on a flat roof, which will provide a natural flow of water into the gutter system. Slab roofing insulation is usually polystyrene, mineral wool and extruded polystyrene foam.
The ideal base for roofing should be firm and even. The screed, which is concrete, cement-sand and asphalt concrete, will meet this criterion.

If you use an asphalt concrete screed as a base, this will make it possible to avoid wet processes that require lengthy drying. Also, this type of screed makes it possible to reduce the installation process of the roof. The probability of waterlogging of the insulation during roofing will also decrease.
During the installation of polymer membranes, mechanical bonding to the base is often used. Using hot air welding with a temperature of about 600 degrees, thermoplastic membrane panels are welded. To do this, use automatic welding equipment. The adjacency device is carried out using a hand-held building hair dryer.
To carry out roof repairs, it is necessary to have such tools, mechanisms and devices:
- electric reversible single-drum winches with a loading capacity of 125 kg;
- Cantilever lifts with a loading capacity of 200 kg;
- metal cantilever beams
- rope with a diameter of 4.8 mm.

Using an asphalt concrete screed, priming the base under the waterproofing layer is not required. The deposited material is laid using the burner flame by melting the primed base and the lower side of the material to be laid. If it is not possible to use an open flame, then ballast or mechanical fastening of bitumen-polymer material can be used.
The modern built-up roof made of polymer roofing membranes or bitumen-polymer compositions is a durable reliable system with a service life of 15-35 years. Repair of the built-up roof will not require additional labor.
Safety precautions
Roof repair with liquid rubber is prohibited during strong winds (more than 6 points), ice and wet roofing. During operation, workers should have safety belts, non-slip (felted or felt shoes), safety belts, safety glasses and mittens.
With any slope of the roof, measures must be taken to prevent the mastic from dripping off the roof and falling materials from it. Do not store primers, solvents, or mastics near fire.
Bitumen boilers must be located on designated special areas that are at least 50 m away from buildings.Near such a boiler should be a set of fire-fighting equipment (dry sand in boxes, a shovel, foam fire extinguishers). The boiler must have a well-closing fireproof cover. Fill the tank with no more than 2/3 of the total volume.
Alas, no comments yet. Be the first!