A knife is a dangerous but useful item. It is impossible to do without it in the kitchen, on a hike, on the hunt, when working on different machines with cutting elements. Any knife must be looked after so that it does not lose sharpness. That is why it is necessary to have at hand a reliable device for sharpening knives. Masters sharpen them on a factory-made grinder, but the simplest device can be made independently. The main thing is to know the specifics of sharpening cutting tools so as not to be mistaken in the calculations.
Content
The Basics of Proper Blade Sharpening
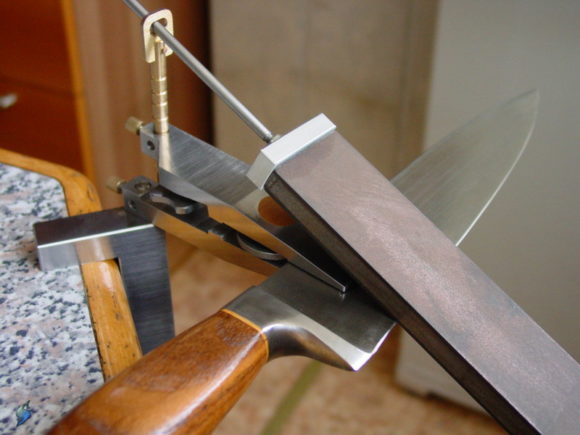
Even housewives have several knives for different purposes. They cut bread and pastries with one device, meat with another, and cut cartilage and bone with a third. There are hunting and fishing knives. Each of them differs from the other in an individual sharpening angle. This concept defines the purpose of the cutting object.
The sharpening angle is visible if the knife did not have time to grind at home. It can be seen when buying a new knife - before its active use.
Manual sharpening of cutting tools is a painstaking task requiring strict adherence to the angle. Factory machines facilitate this task, but are very expensive - from 20,000 rubles and above. If you are a lover of homemade homemade products, you can make a tool for sharpening knives with your own hands, and if you need drawings, you can always find them on the Internet. It will take time, but it will not cost so much. It is known that home-made devices are no worse than factory ones and serve for many years.
Concept of sharpening angle
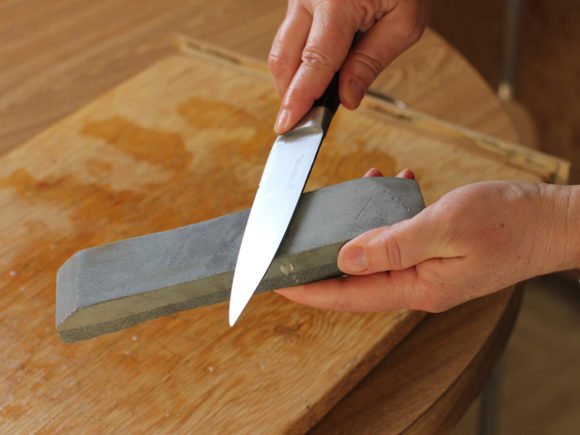
Its value is different for one or another type of blade. The angle dimensions for different cutting tools look like this:
- 8-12 degrees for dangerous razors;
- 10-15 degrees for fillet knives;
- 15-20 degrees for household tools;
- 20-25 degrees for knives for fishing and hunting purposes. Depending on the needs of the hunter or fisherman, the angle may be greater - up to 40 degrees;
- 30-50 degrees for special-purpose blades (for example, for a machete, which is used to cut and chop bamboo, vines and tree trunks).
Whetstone and its features
The process of sharpening knives is impossible without a grindstone. Like emery, it has a different degree of granularity - fine, medium or coarse. This division is arbitrary for different countries. An approximate gradation of the grinding stone looks like this:
- from 200 to 250 - extra-coarse fraction, which is not used for sharpening;
- from 300 to 350 is rough. Blades that are damaged or very blunt are treated with such a sharpener. Also, the coarse fraction is used if you plan to change the angle of sharpening;
- from 400 to 500 - average. It is rare in retail because masters rarely use it;
- from 600 to 700 is shallow. It is these bars that are universal and suitable for most knives;
- from 1000 to 1200 - extra small. With its help, you can give the blade the same brilliance as a mirror.
There are whetstone sharpeners made from diamonds, ceramics or slate rocks. They can be natural or artificial.Bars of natural origin wear out faster than artificial ones. Among them, small-fraction products are rarely found.
Before use, you need to process the bars with water. When absorbing liquid and sharpening, abrasive particles turn into a thick paste. The paste contributes to high quality sharpening. For greater effectiveness, soap mixed with water can be used.
When choosing a bar, it is necessary to take into account its shape and length. The length of the sharpener should be longer than the blade. Most convenient to work on a double-sided grinder, when a fine-grained abrasive is on one side of the bar and coarse-grained material is on the other.
Rules for manual sharpening knives
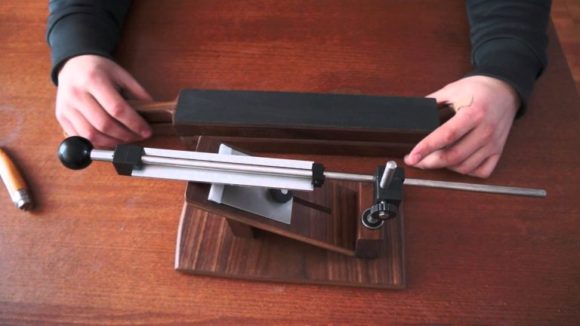
It is impossible to cope with the machine without manual sharpening skills. If you are new to this business, first you need to learn how to sharpen blades using a bar. For hand-sharpened knives, the cutting quality is no worse. The algorithm for working with the bar looks like this:
- lay the bar on a flat surface. Use a medium or coarse grindstone;
- fix it so that during operation it does not fall off the table;
- determine the angle of sharpening (its number will be equal to half of the angle that is selected);
- hold the blade at this angle;
- all movements must be consistent: do not press on the sharpener;
- sharpening start in the opposite direction from yourself;
- make sure that during one approach the blade passes the entire area of the bar. This can be achieved by gently turning the knife handle when the blade approaches the rounded edge of the grindstone;
- After each movement, try to keep the blade on the surface of the stone. Do not let it fall, so as not to dull the knife and not damage it from the side;
- do all movements back and forth consecutively, slowly.
During the process, watch for changes on the inside of the blade. A barb should appear on it. She looks like a thin edge. The burr is carefully groped. In this case, you can not put your finger along the blade. Place your finger perpendicular to the position of the blade on the bar: this will help avoid injury. After finding the edge, start sharpening the knife on the other side so that the burr goes over it and becomes smaller.
After sharpening, change the medium-grained whetstone to a fine-grained sharpener. This will help grind out the remaining edges and smooth the surface of the blade. You can polish the knife so that it will shine no worse than a mirror. To do this, use a bar of fine fraction, and make movements only in one direction, away from you.
Making homemade devices
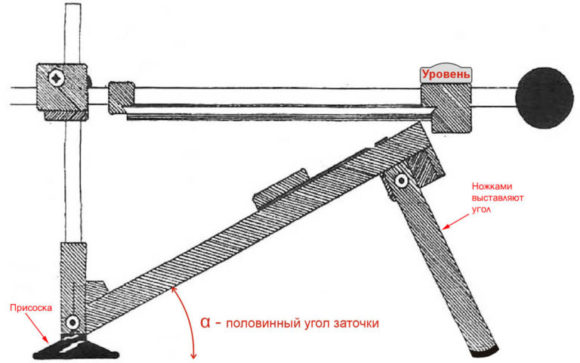
To work with knives, there are different models of “adapt” and full-fledged manual machines. If desired, any of these devices for sharpening knives can be done with your own hands. Sometimes materials at hand that remain after the repair of the house and spare parts from old devices “help out”. Thanks to imagination and ingenuity, craftsmen make both simple and complex devices:
- sharpener "House";
- electric home scissors;
- sharpener LM;
- manual device from a corner frame and a donkey;
- for planing knives;
- for linear processing by bar;
- for jointing knives;
- for sharpening ice drill blades;
- wheeled sharpener.
Sharpener "House"
A simple but effective tool for sharpening. You need to take a small bar with the upper face, in a shape resembling a gable roof. Each face should be inclined at an angle from 20 to 25 degrees. The blade of the knife is tightly fixed to the ridge of the "roof", and its other side is treated with a block or circle in the horizontal direction. Thanks to the roof bar, the angle of inclination always remains unchanged.
Electric Home Slicer
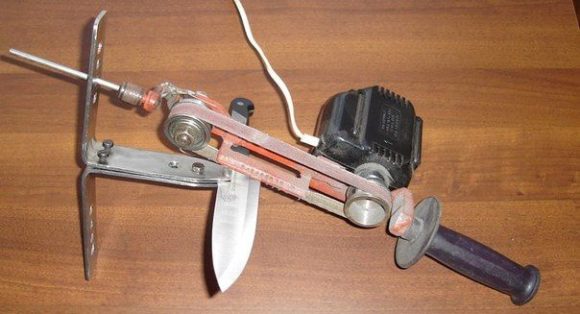
If you upgrade the power plants that you already have at home, you can get an improved modification device. With standard electric sharpening, problems arise with uniform pressure on the blade. To ensure uniform pressure, it is necessary to supplement the design of the machine with a guide mechanism.You will need:
- wooden blocks;
- 4 bolts or as many studs (M8 thread);
- 4 clamping nuts;
- dowels for working with wood.
The guide should be opposite the electric sharpener. A runner moves uniformly along it. Guide rail fixing place: workbench or prefabricated bed. In the bed for her mobility, a groove is cut out in the longitudinal direction, and the tripod is fixed with two studs. Side holes are drilled in two blocks, then one pin is inserted into them and tightened with clamping nuts.
Fixing devices are attached on both sides of the movable carriage. When sharpening, the carriage is set at the desired height, fixing it with clamping nuts. The tripod is adjusted depending on the size of the cutting tool, which in the process is moved along both guides.
Sharpener LM
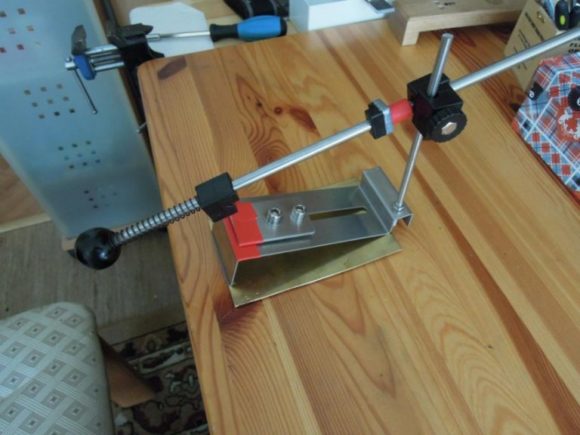
The Lansky Metabo sharpener is difficult to manufacture. Most often, professional grinders work with her. To work with such a project, drawings are needed. It is designed so that the angle of sharpening can be changed depending on the type of cutting tool. Its clamps are designed in such a way that when fixing the root part of the blade in them, you can achieve the maximum sharpening angle. The LM sharpener is often used for sharpening jointing knives and thicknessers, and the clamps are made of blocks or metal corners.
With the self-assembly of such a design, many difficulties arise - due to the large number of complex elements.
Manual device from a corner frame and a donkey
It’s better not to try to assemble a complex machine straight away, but to stop with a simple tool. From improvised means, you can make a kind of angular structure with a built-in donkey. When supplementing the device with a carriage, there is no need to constantly maintain the sharpening angle manually. For the carriage, you need a triangular bar and a magnet that will attract a metal blade to itself.
Sharpening planing knives
A device for sharpening planing knives is a rare occurrence. It is almost impossible to buy such a machine, so the craftsmen are engaged in the improvement of those machines that are initially available. To create a “planing” device, you will need the usual low-speed sharpener with water cooling. As a grindstone, fresh, unused material of a large fraction with a flat surface is used.
Device for linear processing
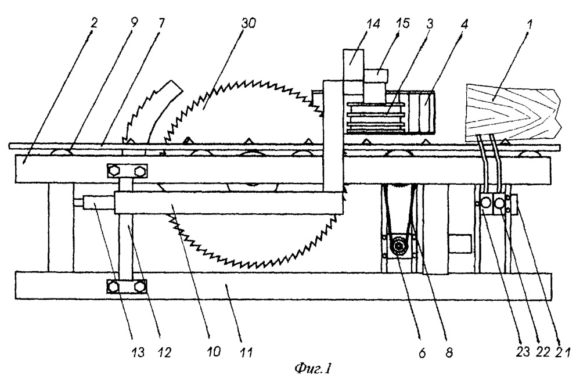
A device for linear processing with a bar is a complex model of a machine that a person with experience in carpentry can handle. Have to take:
- plywood or particleboard coated with a laminate;
- a hairpin made of steel with a "long" thread (diameter of the stud is from 6 to 8 mm);
- textolite or ebonite block (either wooden, from oak or beech);
- aluminum plate (plate thickness from 3 to 5 mm);
- fastening nuts;
- Neodymium magnet.
The base of the machine is assembled from plywood. We establish a bed on legs. In the lower part you need to twist a long hairpin, and its balance carefully cut. We fix the aluminum plate in the middle. A groove should be made in it, the diameter of which corresponds to the bolt. Aluminum is a soft metal that does not harm the blade, therefore, it is not recommended to use other material.
Emery or whetstone must be attached to the machine with the lever. It can be made from the part of the hairpin that remains. The devices that fix the bar are cut out from the PCB, and the stop is fixed with a nut. Where the handle is located, it is better to spring up the unit immediately. Such a mechanism will facilitate the replacement of the old sharpener with a new one. After springing the block onto an aluminum plate, glue emery or sharpener. Depending on the area of the working surface, the number of sharpeners of different fractions can be from 2 to 3.
The advantage of this machine is its movable joint, which has two degrees of freedom. It is collected from two textolite bars of the same size.The first bar is mounted on a hairpin located vertically. This is necessary to create a horizontal axis when turning the blade, and also in order to adjust the height of the lever. This design always ensures the right grinding angle.
In the second textolite bar, a hole is made in the horizontal direction - for the lever. After this, the second block is screwed to the first, and the lever will move freely vertically. When sharpening, the knife is clamped with a plate or a neodymium magnet is used.
Device for knives jointer
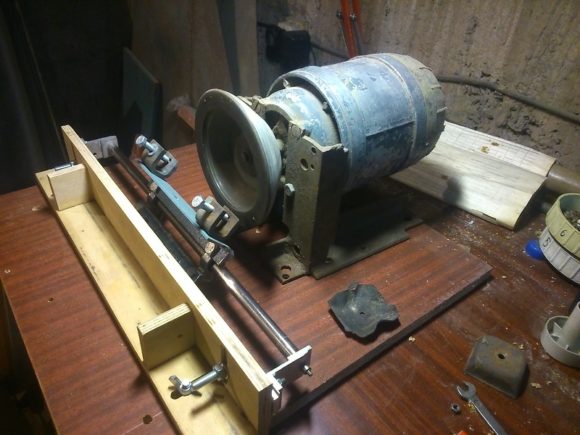
The device for sharpening knives of the jointer is mounted on a vertical type milling machine. The device is made of two plates. The first is located below, the second is above. The holder in which the blade of the cutting tool is placed is located on the top plate. To fix the bottom plate to the base of the milling machine, a clamp and metal corners are used.
For the holder of the jointer knife, you will need clamps and a metal corner (50x50 mm). It is cut at a sharpening angle of 40 degrees. The edge of the jointing knives should be strong, and the grinder should be lowered to a shallow depth (about 10 microns) so as not to damage it during operation. The upper plate of the device is lifted by a mechanism, which includes a wedge, lead screw and plates for stop. During the rotation of the handle, the lead screw and wedge begin to move: you can raise the top plate or lower it down.
How can I sharpen icebreaker knives
A device for sharpening knives of an ice drill can also be done at home. It is necessary to take two strips of steel, each of which has the following dimensions:
- thickness - from 3 to 4 mm;
- width - from 50 to 60 mm;
- length - from 160 to 200 mm.
Strips are needed to make the device case. One of them is bent in an arc. This is necessary for the correct position of the knife chamfers. They must be in the same plane. In this position, the sharpening angle of all knives sharpened simultaneously will be the same. After manufacturing the body arc from the second strip make the plate, which is needed to fix the cutting tools.
Next, in the plate and in the body you need to drill through the hole. We insert bolts with an M12 or M14 thread into each hole. Using a bolt and nut, we fix the plate to the body. Now we need to try to clamp the knives between the body and the plate and check their fit. The contact of the blades to the end surface must be accurate and tight. If the chamfers are not tight enough to the abrasive “sharpener”, the sharpening angle will be incorrect. To correct it, the body arc is “adjusted”, slightly bending it in the desired direction. If everything is done correctly, you need to disassemble the structure and weld two stiffeners (one on each side) to the body arc.
Sharpening knives for ice drill is best done on an abrasive wheel that rotates in the horizontal direction. When the knives are moistened with water, in this position the liquid will stay longer in a circle. This technology helps maintain the abrasive wheel and helps cool the steel blades.
The ice drill sharpener is ready. In order to avoid overheating of the metal during operation, it is necessary to lower the knives into the water more often.
Wheeled fixture
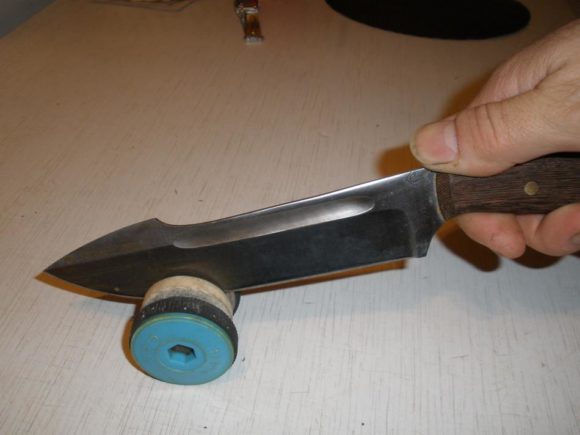
A simple wheeled device is a structure that consists of a fixed bar and a cart with wheels. During sharpening, the knife moves the knife blade manually, and the sharpening angle is determined by the height at which the block is located in relation to the work platform. A blade is placed on the platform and fixed. The device on wheels is used only on a flat surface.
Since we are talking about the simplest device, the sharpening angle during operation may vary slightly. The device is designed to work with household kitchen knives, so changing the angle in this case is not fatal. If you improve the design with two or three holders, the angle will be almost perfect.
Using simple elements of wood and metal, you can make any device for sharpening kitchen knives. Most often, you don’t need to design complex machines for domestic needs, but if you have a ready-made milling machine at hand, craftsmen can adapt it to work with more complex cutting tools.
Alas, no comments yet. Be the first!