High-quality thermal insulation, performed on the roof of the building, is one of the important points, since it is it - this is a guarantee that a significant part of the heat will not be lost through the floors of the upper floors. Incorrect arrangement of the roofing cake leads to the fact that the rooms located on the last floors of the buildings require more intensive heating, which ultimately gives a very significant increase in heating bills. It is possible to avoid such a problem even at the design stage, when the roof structure is being developed: it is at this stage that it is decided whether such technology as thermo-roof will be used or not.
It significantly increases the comfort of living in the house and reduces energy costs for heating large buildings. Such material can be used not only during the creation of a new building, but also during the overhaul of an old one. This is one of the foundations of modern construction, so below we will try to tell in detail about the production, installation and operation of such material.
Content
What is thermal roofing
By this term is meant a technology that involves the use of one of the types of stove insulation. The most common option is compressed mineral wool, but polystyrene boards are also found. In fact, mineral wool can be produced from several types of raw materials, so we will describe only the general manufacturing technology, without going into details of how the material from which the thermo-roof is made is obtained.
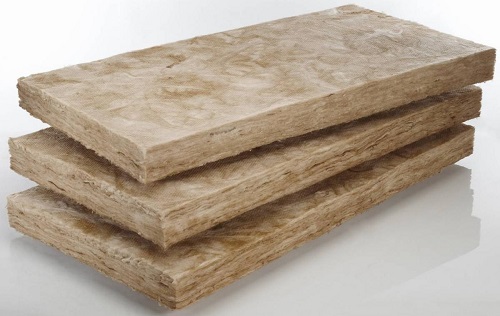
The technology of creating insulation can be imagined as obtaining ultrafine fiber drawn from a melt of various rocks. After receiving a sufficient number of individual threads, they are interconnected using a binder. The following stages of work can be distinguished:
- raw material preparation;
- molten mineral materials;
- fiber production;
- binder input;
- binder polymerization;
- insulation cutting.
The resulting material is used when it is planned to create a classic version of a flat warm roof, but there are also inverse varieties of it. In this case, expanded polystyrene having high thermal insulation characteristics can be used.
Inversion ThermoBlood
Anyone who has visited the megalopolises of Southeast Asia or took the time to admire the panoramas of Tokyo has repeatedly paid attention to the fact that the roofs of buildings are used and, moreover, very actively. We will not talk about the reasons for this, but we will dwell on the technology itself in more detail. We are talking about the so-called inverse roof, which is a "puff", performed on top of a reinforced concrete slab. This technology can be implemented through the use of such a solution as a thermo-roof.
All necessary work can be divided into stages:
- installation of waterproofing coating;
- installation of insulation plates;
- laying of geotextiles;
- backfill;
- installation of the root layer;
- topcoat.

The last two points suggest the creation of a lawn on the roof, but other options are possible. In each case, certain operations will be required to ensure the reliability of the laid coating.
Installation of waterproofing material is carried out directly on the concrete slab.It acts as the last frontier, protecting concrete from moisture, which can penetrate through the insulation layer. Of course, the concrete itself carries moisture, albeit not always well, but the roof has seams, abutments, exits, which are a potential problem.
Waterproofing is a single-layer coating performed directly on top of concrete using guided material. The roll is heated by a gas burner and unwinds on the roof. In order to exclude the possibility of leaks, adjacent layers are superimposed on each other with an overlap of more than 100 mm.
This type of thermo-roof is created using URSA XPS insulation boards, which are laid end-to-end.

Due to the special porous structure, URSA XPS boards easily tolerate contact with water. The liquid cannot penetrate the volume of the plate if the latter is not damaged, which means that the properties of the material will be preserved in full. I must say that the plates themselves are connected not end-to-end, but by means of a figured groove, and therefore there will be no road for water.
The thermo-roof is protected from water penetration due to the Z-shaped joint, which securely fixes the expanded polystyrene boards relative to each other. The finished coating has thermal engineering uniformity. On top of this material rolls of geotextiles are deployed, the task of which is to prevent siltation of the drainage channels and their clogging with soil particles or a fine fraction that is part of the cargo. If you do not use such a cloth, then the inversion-type thermal roof will begin to silt, and there will be no removal of moisture from its surface.
The load is a structural element of the roof, the task of which is to protect the insulation from high wind loads. Crushed stone of small fractions, evenly distributed over the entire surface of the roof, is usually used. The layer thickness is selected in accordance with the project, according to which a thermo-roof is created. On top of the cargo is the penultimate layer - geotextiles, which have increased strength. The objective of this material is to protect against plant roots. He himself lets water through, but the body of the structure is reliably protected from the formation of unplanned inclusions.
Other types of inverse roofing
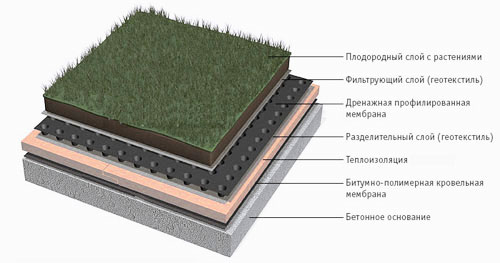
In this case, the thermo-roof has a green finishing layer - this is a lawn grass that covers most of the roof surface, forming a small green lawn on the roof of one of the city skyscrapers, or allowing you to take your country house one more step closer to wildlife. However, there are other types of coatings.
The main difference between the inverse roof is that the service life of the entire structure is determined by the durability of the waterproofing material. Of course, there are a number of reservations, for example, the absence of temperature differences or significant concentrated mechanical loads. But for ordinary waterproofing, such conditions are hothouse, so it, and with it the thermo-roof, can last at least 30 years. It should be noted that a special solution is being developed for each climate zone, since in the regions located closer to the north, additional protection for waterproofing is required.
Thermoblood can and can be made of:
- asphalt concrete;
- paving slabs;
- crushed stone dumping.
Crushed stone filling is crushed stone of small fractions, which will be evenly distributed over the roof surface. This is an inexpensive option, which is suitable for cases where this section of the roof will not be used as a platform for anything. Thermal roofs covered with pebbles or gravel are also not used near the sea, as the house will become too attractive for winged guests.
Asphalt concrete is a mixture of crushed stone, gravel and fine aggregate with a bitumen binder. It is of several types and is widely used in the construction of roads, engineering structures, airfields, etc.This material has high performance characteristics, so such a thermo-roof will bear any adversity that has fallen to its lot.
Paving slabs are no less attractive, and it is of particular interest for arranging your own housing, since on the roof you can create almost any pattern and fully realize one or another designer's plan.
Classic ThermoBlood
This is not a heater from expanded polystyrene plates, but mineral wool, with which we began the story about the features of thermal insulation of flat roofs. The installation technology of this material is somewhat different from the method of inversion roofing described above.

Mineral wool plates are used for thermal insulation of flat roofs having a multilayer coating of profiled sheet or reinforced concrete plates, where a rolled roofing carpet is used. An alternative use case is a thermo-roof, created with a minimal slope of the slopes in one layer, on top of which a screed made of sand concrete is arranged.
One of the features of using this technology involves the creation of a certain slope for the roof. We considered this issue in the corresponding article, so we will not dwell on it in detail. Thanks to a slight bias, it becomes possible to:
- increase the reliability of thermal plates;
- reduce the likelihood of deflections of the metal sheet;
- protect the roof covering from damage during deformation of the insulation plate.
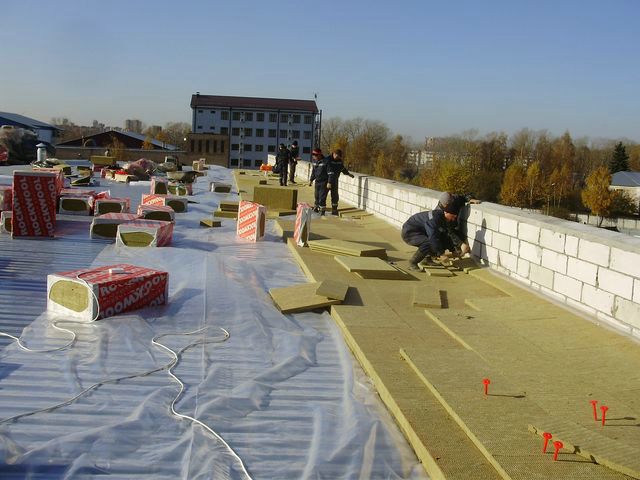
An important difference of the mineral wool sheet is that it is afraid of water. Those. moisture easily penetrates the structure of the material, so cold bridges are formed, and the thermo-roof itself does not cope with its task. It is not difficult to get around this problem, it is only necessary to protect the plate material according to the same scheme that is used in pitched roofs. In this case, the vapor barrier is located below and the waterproofing layer above.
When using a reinforced concrete base, it is recommended to use bituminous surfaced materials, and under the metal profile a thermo-roof is created with bitumen-polymer rolls, the basis for which is polyester.

Installation of vapor barrier material does not depend on the type of supporting structure and is carried out directly under the layer of thermoplates. This structure is the most reliable option for those cases when mineral wool insulation is used.
The technology by which the classic thermo-roof is created involves the use of special binders or bitumen of a suitable brand. Reliability and solidity of the coating can be achieved thanks to careful bonding and verified dimensions of the elements. To avoid problems at this stage, when using a profiled sheet as the base, it is recommended to choose the joints on the shelves, and not in the deflections of the wave.
In this article, we talked about the two most common approaches, using which a reliable thermo-roof is created, and a little highlighted the technology for producing insulation from mineral fiber.
Alas, no comments yet. Be the first!